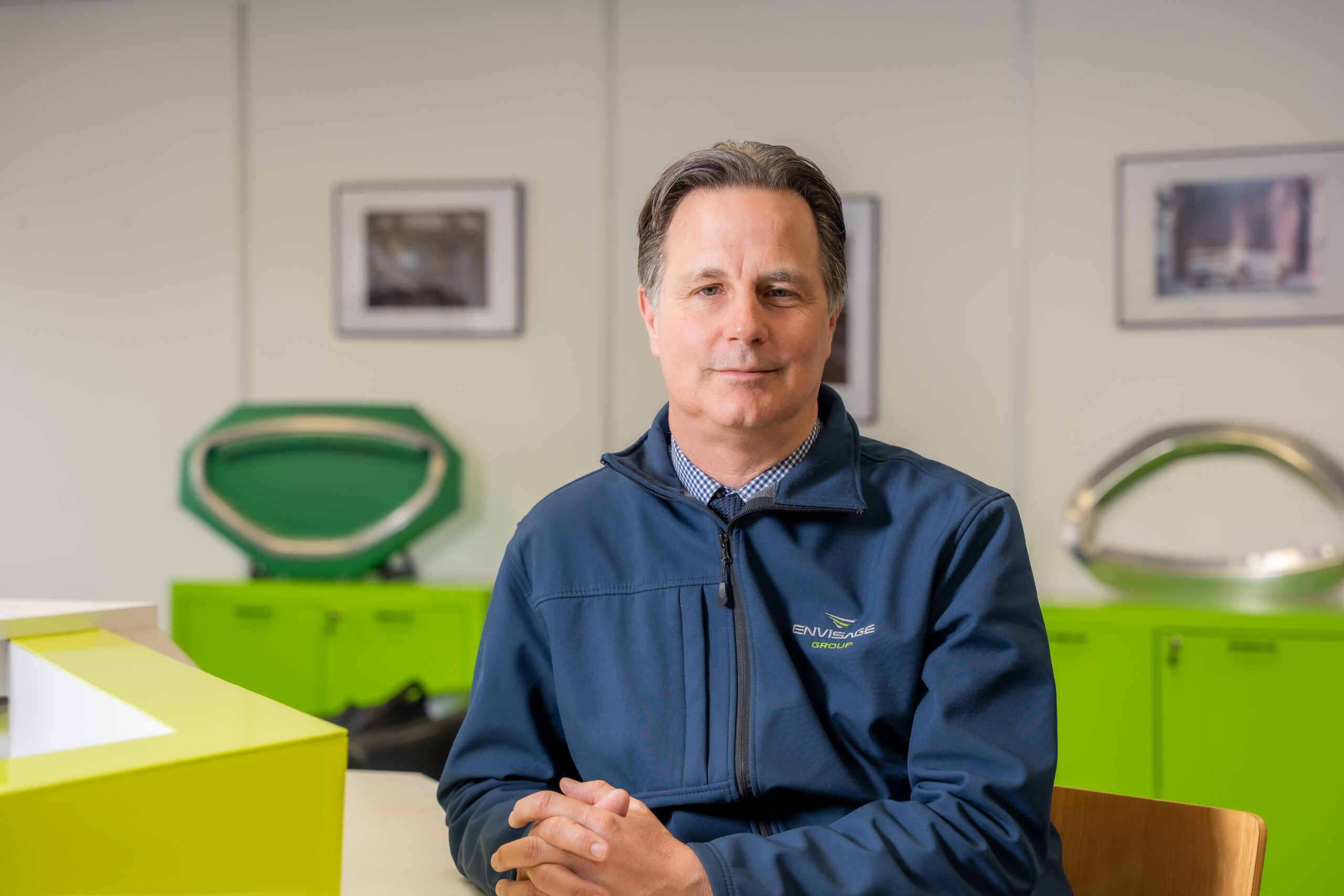
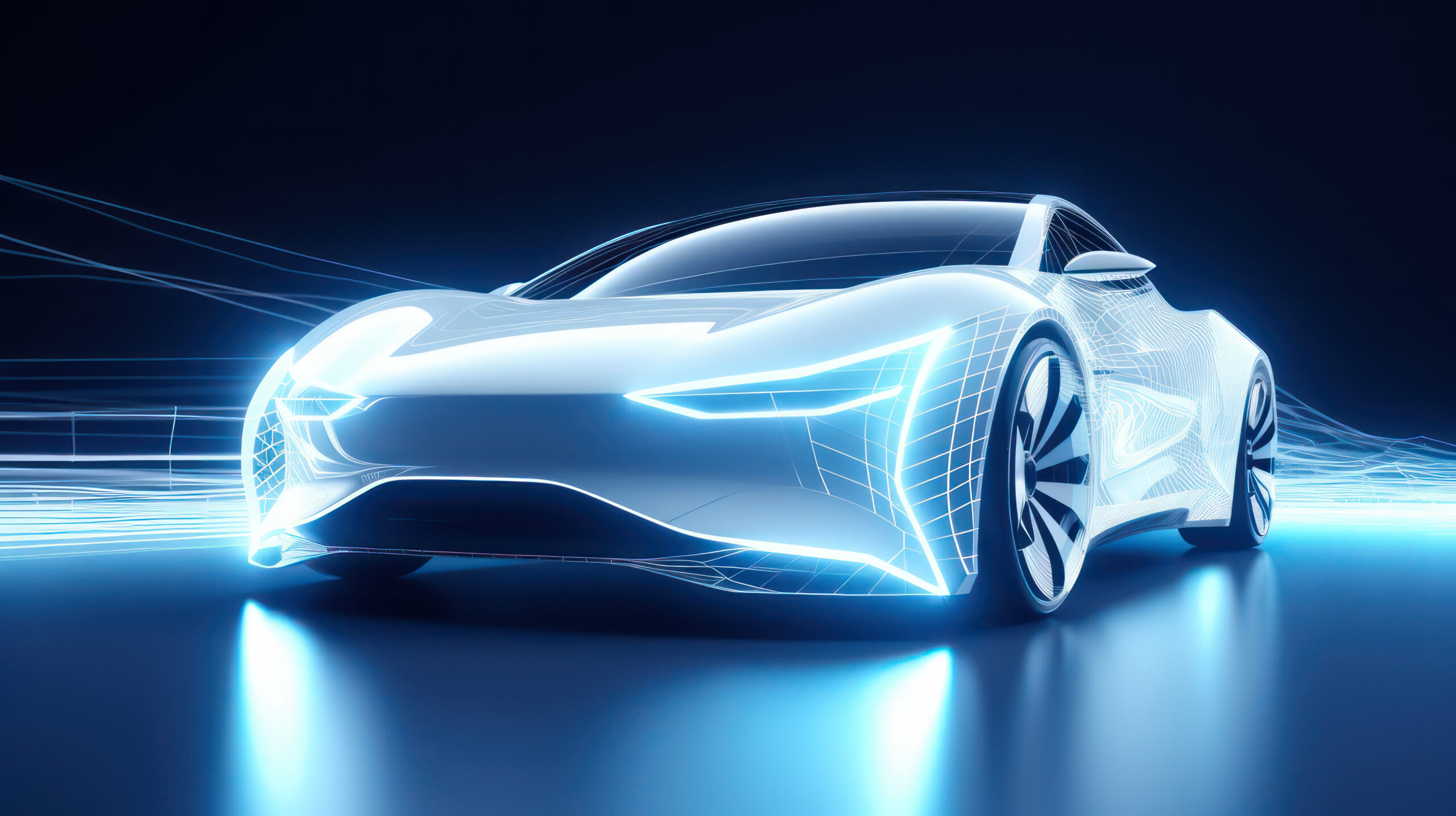
Dimensional Engineering
Envisage Dimensional Engineering utilises a structured approach to dimensional system design from concept to production.
Benchmarking
Envisage can conduct gap and profile benchmarking studies, we will work with design and engineering teams to guide the target specification for new vehicles.
Our dimensional engineers advise on parts of the process tolerances that are applicable in automotive applications from a broad range of processes including stamping, moulding, casting, and machining.
This enables more accurate concept feasibility confirmation at the early stage of programmes.
Gap Plan
We are experienced in the creation and management of interfaces which look at the identification of priorities, section book set up, proposing competitive targets, target validation (DVA) and change management with product development.
This is all achieved in consultation with the customer’s design and engineering teams.
Functional Objectives
Defining dimensional targets for functional systems on the vehicle is critical to ensue reliability and durability of the finished vehicle. It is also a critical input before commencing the system design to understand priority measurement points.
Our dimensional engineers assist engineering teams to derive targets for their systems, capture measurements and validate targets through simulation. Some typical functional targets are:
- Chassis Geometry
- Sealing
- Mounting of major assemblies
- Packaging clearances
- Sensor angles
Body Dimensional Brochure
Body structure is critical to the dimensional performance of most vehicle systems. Vehicle functional systems have a cascade of requirements to the body structure to achieve functional objectives.
A “Body Dimensional Brochure” is created at the start of the programme and updated during the vehicle programme. Requirements are captured in the “Body Dimensional Brochure” and used to design the assembly of the body structure.
Assembly Concept
We can support the development and definition of the assembly concept for each system. Together with manufacturing engineering and/or suppliers each relevant part is defined in sequence and assembly level.
Datum Concept
For every part and assembly in the system, we define the mounting and GD&T concept. Datum selection will be conducted in co-operation with customers engineering and manufacturing teams. If there is no clear direction, our engineers will propose a concept for approval that meets functional and/or cosmetic targets.
Component GD&T Manufacturing Capability
Before starting tolerance simulation activities for each part, assembly and fixture is defined with tolerance information. Typically, there are three levels to maturation of tolerance inputs.
- Envisage proposed.
- Customer engineer agreed.
- Supplier/Manufacturing agreed.
Based on our experience we propose tolerances that most suppliers are able to deliver but there are occasions after nomination that suppliers request tolerance changes.
Tolerance Simulation Modelling – Dimensional Variation Analysis (DVA)
We will conduct tolerance simulation (DVA) in 3D, 2D and 1D. Most 3D simulations are modelled in 3DCS software. The simulations are based on the definition of parts and process conducted during the concept phase.
Design Optimisation
We have capabilities in the analysis of tolerance simulation results to optimise the design and manage variation. At this stage of our process, we would go through the following hierarchy of optimisation:
- Elimination of requirement.
- Change to datum structure – analyse different datum concepts for more stability and minimise. geometric effects.
- Change assembly process and/or use of fixturing.
- Change part design – e.g., split parts/join parts.
- Change material/part tolerances.
- Change target.
Costs and feasibility typically increase from top to bottom.
Drawing Release
We can conduct drawing checks of released drawings. Dimensional Engineering would be checking:
- Datum concept and tolerance values are consistent with GD&T on the drawing.
- GD&T on drawings is correct and meets customer standard or international standard (ISO/ASME).
In addition, we can provide training in GD&T and drawing standards.
Validation
We are experienced in design and manufacture of inspection fixtures to validate components and assemblies.
- Body Maturation – blue buck and fixtures, offering dimensional stability which allows parts to be tunes to fit the production body.
- Trim Maturation – ‘E’ Cube (interior/Exterior/Lighting/Closures/Electrical), cubes will have multiple quality loops and can switch to tune parts after. Strong variability control in OEM and Suppliers.
Contact our Dimensional Engineering team directly
Contact our Dimensional Engineering team directly
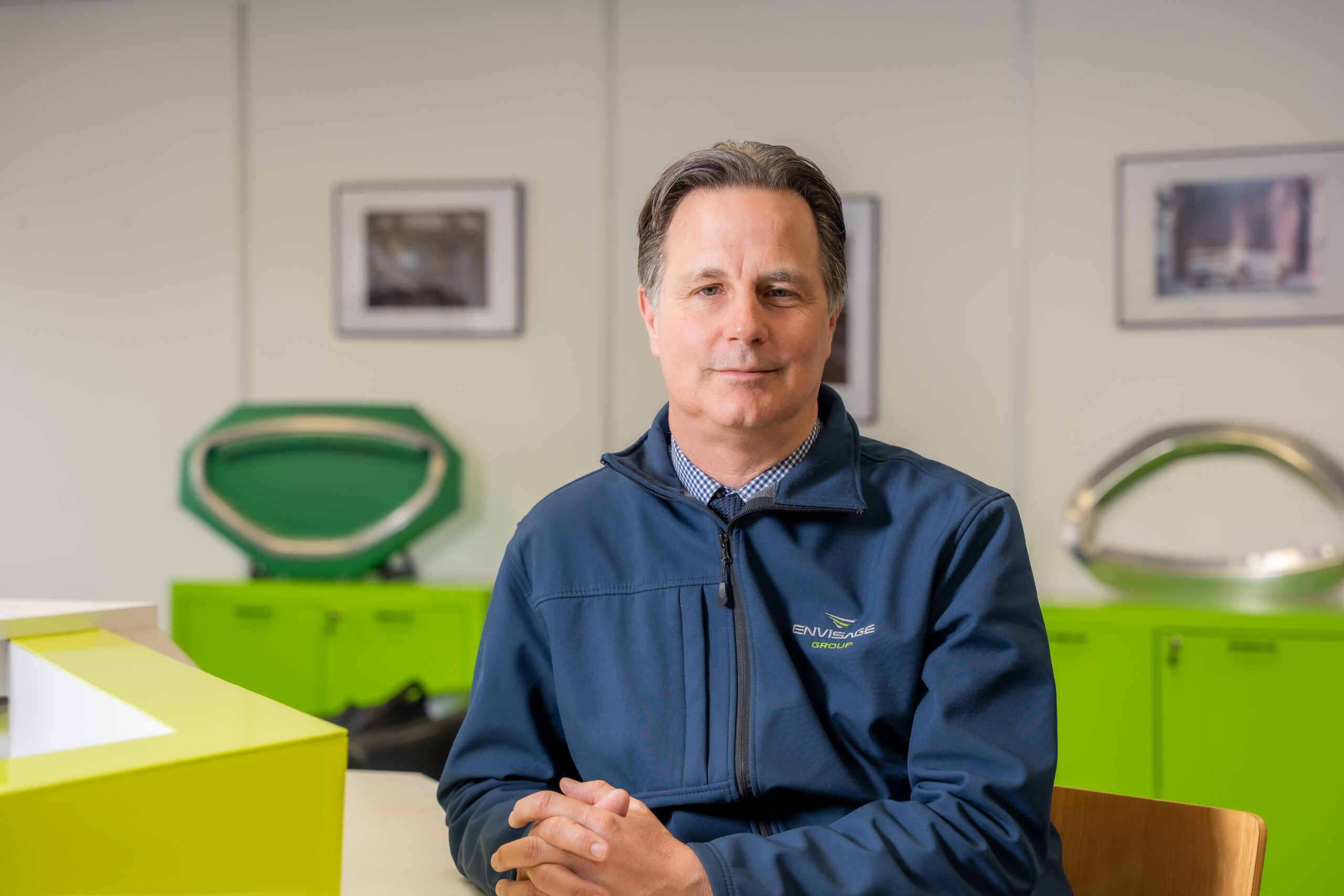